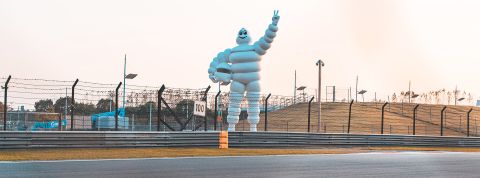
Dans un contexte économique difficile, les industriels tirent les leçons de la pandémie et de la guerre en Ukraine. Au programme : résilience, digitalisation des processus et accélération de la réindustrialisation des territoires.
Cet article est extrait du Livre des Tendances 2023, 20 secteurs clés de l'économie décryptés
L'industrie est à un tournant. D'un côté, le numérique augmente l'efficacité des unités de fabrication, garantit un plus haut niveau de qualité des produits, des délais de commercialisation plus courts. Les capteurs, les données et les algorithmes optimisent les flux logistiques, avec de très nombreux bénéfices à la clé. C'est un puissant facteur de changement.
De l'autre, les crises systémiques, qu'elles soient climatiques, sanitaires ou politiques, obligent les entreprises à repenser la répartition de leurs unités de fabrication et de leurs fournisseurs dans une optique de démondialisation. Un enjeu qui leur permet aussi de réduire l'empreinte carbone de leurs activités. Ces transformations de fond doivent se faire dans des contraintes économiques défavorables.
Des perspectives incertaines
Pour les acteurs français, le début d'année 2022 a été synonyme de dynamisme retrouvé. Selon une enquête de la chambre de commerce et d'industrie en France, 2021 aura été marquée par 87 retours d’entreprises sur le territoire national, contre seulement 16 délocalisations, 32 155 créations d'emplois contre 16 000 postes supprimés, et 176 projets d’ouverture de sites industriels. À cela, il faut ajouter que les exportations françaises de biens manufacturés ont progressé de 5,3 % au premier trimestre 2022, confirmant les bons résultats déjà enregistrés fin 2021 avec une hausse de 4,7 %, selon les chiffres fournis par le Département des statistiques et des études du commerce extérieur. Ailleurs dans le monde, la dynamique était la même, avec une croissance globale de 3,3 % pour la fabrication et la commercialisation de biens manufacturés au premier trimestre. Après deux ans de pandémie, l'industrie mondiale reprenait enfin des couleurs.
Cependant, la guerre en Ukraine, ainsi qu'une nouvelle vague de confinements en Chine, est venue gripper cette belle mécanique en entraînant une décélération de grande ampleur. Très dépendants de la stabilité des prix de l'énergie, et pour certains d'entre eux des métaux russes, les industriels ont vu leurs capacités de production fléchir quand leurs circuits d'approvisionnement en matières premières ont été en partie mis à l'arrêt. Pour ne rien arranger, les tensions géopolitiques portant sur le statut de Taïwan ont fait peser un risque sur les exportations hautement stratégiques de semi-conducteurs. Preuve que le choc a été brutal, l'indice PMI (Purchasing Managers Index), l'indicateur le plus suivi au monde, a chuté de plusieurs points au deuxième trimestre en Europe, tandis que le PIB mondial se contractait. Un mauvais signal pour l'avenir.
Dans ce contexte, sécuriser les chaînes de valeur est devenu un impératif pour chaque entreprise. Pour y parvenir, les mutations en cours promettent un plus haut niveau de résilience, mais aussi une plus grande capacité à la réindustrialisation.
La réinvention de la supply chain
Véritable enjeu stratégique pour tous les acteurs, la supply chain est en train de connaître des bouleversements majeurs. Fait marquant, selon l'édition 2021 du baromètre de l’industrie mondiale réalisé par le cabinet Trendeo, les distances d'approvisionnement en pièces détachées et en ressources diverses ont tendance à nettement diminuer, avec une baisse de 5 % des kilomètres parcourus par les importations à travers le monde. Ce phénomène s'explique par la relocalisation d'un nombre croissant de sites industriels, mais aussi par une nouvelle approche de la supply chain.
En amont, l'économie circulaire est, en effet et de plus en plus, considérée comme un moyen de garantir les approvisionnements stratégiques. De fait, pour faire face à la hausse du prix des matières premières et à leur disponibilité volatile sur les marchés, aussi bien en raison de la guerre en Ukraine que du réchauffement climatique, un nombre croissant d'industriels misent sur le réemploi pour fabriquer de nouveaux produits. Ainsi, Saint-Gobain utilise, à hauteur de 20 %, du gypse recyclé dans ses plaques de plâtre, tandis que Michelin transforme par pyrolyse ses pneus usagés, afin de produire du carburant. La circularité garantit la disponibilité permanente des ressources, tout en générant moins de déchets, et donc moins de CO2.
En aval, l’e-commerce et les enjeux du dernier kilomètre font évoluer la gestion des flux avec l'injonction de répondre toujours plus rapidement à la demande, et ce sans polluer. Pour les industriels, l'adaptation à ces nouvelles règles est désormais une condition sine qua none pour vendre leurs produits. En conséquence, les entrepôts de stockage passent le cap de l'automatisation pour gagner en efficacité, faisant circuler dans leurs allées convoyeurs autoguidés et robots de palettisation, et misent sur les énergies renouvelables pour limiter les émissions de CO2, comme c'est déjà le cas pour ceux de L'Oréal dans le Nord. La logistique intègre pleinement le numérique et la durabilité dans son logiciel, pour mieux satisfaire les clients et gagner en sobriété grâce à un fonctionnement optimisé.
En parallèle, la relocalisation des sites de production favorise l'émergence d'une supply chain durable, car elle rapproche le lieu de production du lieu de consommation, recalibrant à l'échelon local la cartographie des circuits d'approvisionnement et de distribution.
La résilience des lignes de production
Autre facteur d'amélioration pour l'industrie, l'anticipation des pannes et des défaillances gagne du terrain. C'est même devenu un enjeu crucial. En effet, dans l'étude « The True Cost Of Downtime » réalisée en 2021 auprès de 72 entreprises internationales, le spécialiste de la gestion intelligente des équipements Senseye révélait que la mise à l'arrêt d'une ligne de production pendant une heure générait un manque à gagner moyen de 450 000 euros, et que ce chiffre grimpait à 145 millions d'euros par an pour les sites industriels de grande envergure. Un véritable gouffre financier.
Plus problématique encore, une autre étude menée à la même période par le cabinet de conseil Aberdeen Strategy & Research indiquait que le nombre de pannes avait augmenté de manière significative dans le secteur industriel ces cinq dernières années, touchant 90 % des acteurs, contre 82 % en 2016. Mais la réponse existe…
Aujourd'hui, grâce à l'implémentation croissante de l’IoT dans les chaînes de fabrication et aux progrès réalisés par les algorithmes d'intelligence artificielle, la maintenance prédictive donne la possibilité de connaître les risques de défaillance d'un équipement, et de les corriger avant qu'elle ne se produise, en identifiant, grâce aux données, les signaux propres à une détérioration. En outre, le machine learning permet désormais de regarder au-delà des schémas d’anomalies préalablement identifiés pour en ajouter de nouveaux au fur et à mesure de la collecte des informations. Et d'avoir ainsi un coup d'avance supplémentaire.
De plus en plus, l’utilisation de capteurs et d’actionneurs intelligents fiabilise les processus industriels alors que le nombre de solutions proposées ne cesse d'augmenter. Selon le cabinet McKinsey, la maintenance prédictive pourrait permettre aux industriels d'économiser 630 milliards de dollars d'ici 2025.
En complément, l'impression 3D apporte également une couche de résilience en permettant de façonner rapidement et à moindres frais une pièce détachée manquante. Elle garantit aux lignes de production de ne pas être freinées par un défaut d'approvisionnement. Selon le rapport « State of 3D Printing » rédigé en 2021 par l'entreprise néerlandaise Shapeways, 68 % des industriels considèrent que ce procédé représente le futur de la fabrication.
Avec pour point commun de réduire la fréquence de renouvellement des pièces détachées et des composants, et donc mécaniquement de faire baisser les coûts de production, ces technologies renforcent l'autonomie opérationnelle des industriels et les rendent moins dépendants de leurs prestataires. C'est un atout pour favoriser le retour des usines à proximité des consommateurs.
Vers la réindustrialisation profonde ?
Pour répondre aux enjeux climatiques et aux tensions géopolitiques, la relocalisation permet de rediriger la production des biens manufacturés dans une trajectoire vertueuse et sécurisée. En parallèle, la transformation de l'industrie tend vers un fonctionnement de plus en plus indépendant.
De fait, en resserrant les distances d'approvisionnement, en contractant l'éparpillement des sous-traitants, et en misant sur la circularité, l'usine de demain pourrait gagner en indépendance, en efficacité et en sobriété. À l’avenir, la réimplantation d'un nombre toujours plus élevé d'unités de fabrication au sein des territoires pourrait favoriser l'apparition d'une nouvelle géographie industrielle qui aurait pour vertu d'être, au moins en partie, démondialisée. Ce serait une transformation radicale pour le secteur.
Participer à la conversation